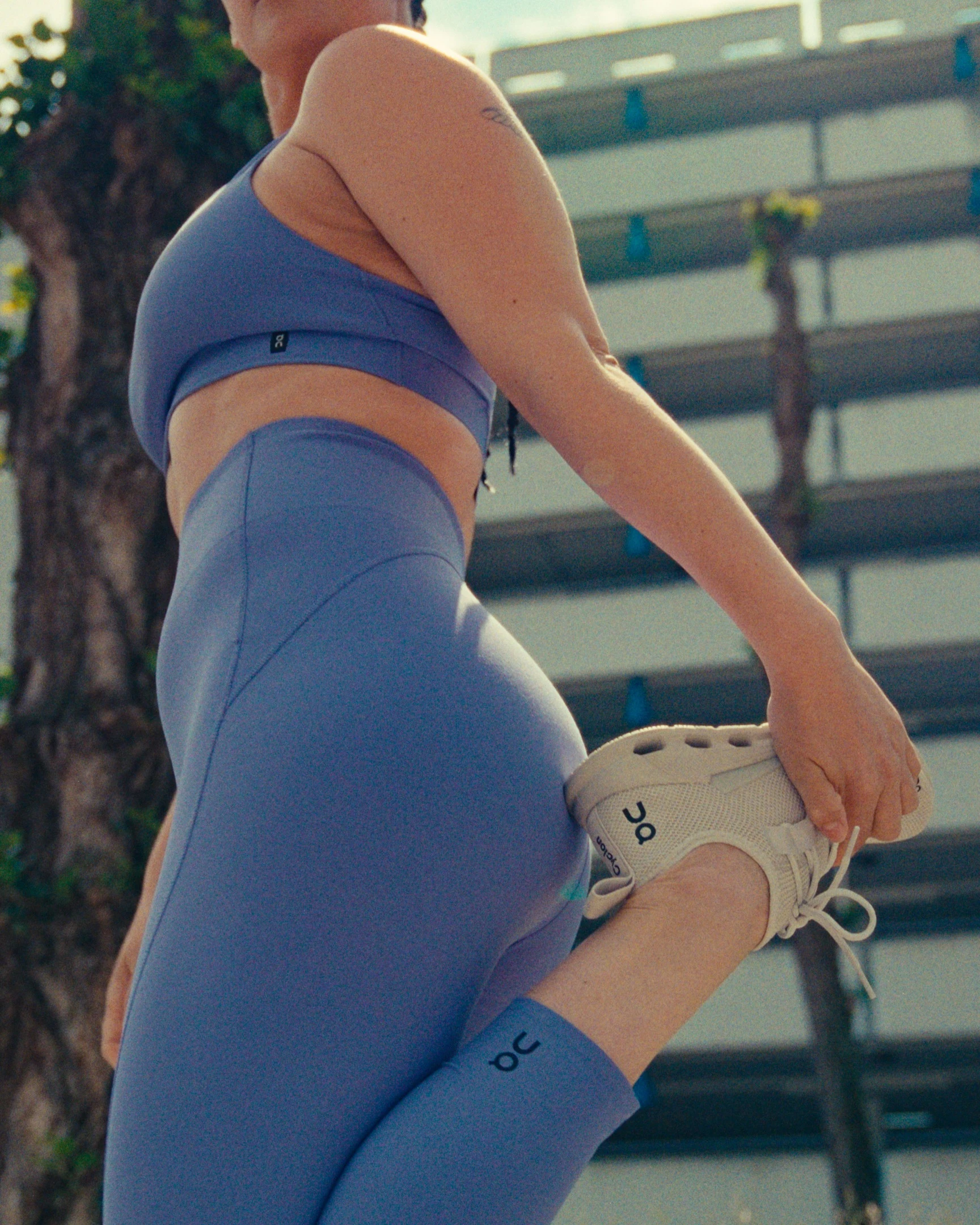
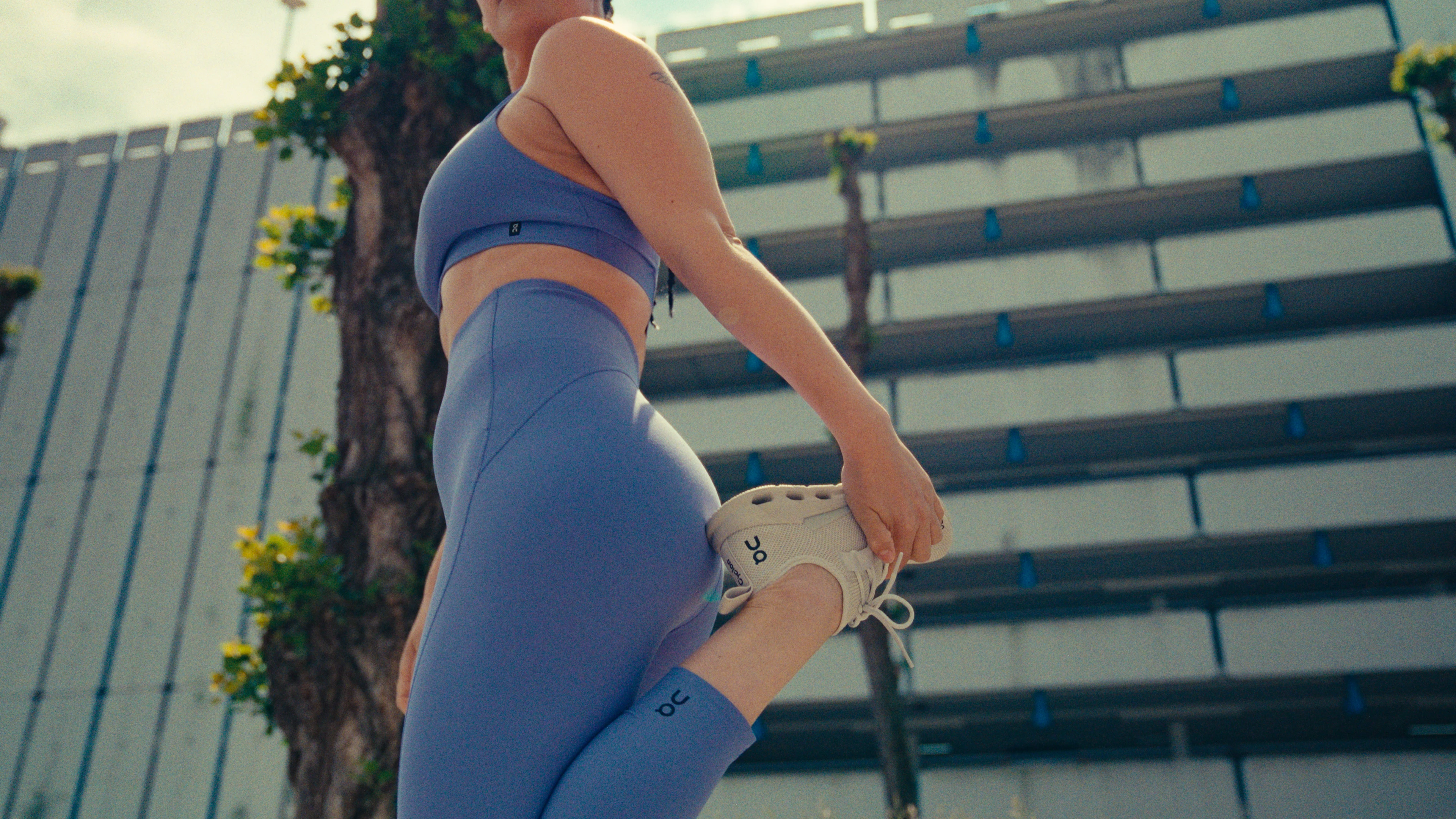
A conversation exploring opportunities and challenges around fiber-to-fiber recycling, and further embedding circularity into On’s processes, designs and business models.
Words by Laura Markwardt. Photography by Noah Steiner.
Dana Müller: Franchise lead for Cyclon™ Georg Singer: Innovation Business Development Daniel Solomita: CEO of Loop Industries
‘Conventional recycling’ as a catch-all, one-word solution to a global issue of finite resources, overconsumption and mounting waste, has its limitations.
Generally, it’s considered the reintegration of materials into a production cycle that would otherwise be thrown away as waste. This works well for pure products like clear PET plastic bottles, but becomes more challenging for products made of mixed materials or colored and opaque plastics.
In the textile industry, conventional recycling relies on plastic bottles and packaging waste made of polyester (PET) that is downcycled into recycled polyester textiles. PET (which is normally fossil-fuel based) is one of the highest volume materials used in sportswear, not only at On, but globally, across the apparel industry. Research from The Textile Exchange confirms that in 2023 alone, around 99 percent of recycled polyester in the global market came from PET bottles which were downcycled.
There’s growing awareness that almost every piece of apparel made from recycled PET bottles eventually ends up in landfill or incineration. We need a new approach.
In theory, this means reducing our reliance on plastic bottles as a first source of recycled material, and driving forward solutions that make the textile and footwear industry more circular.
In practice, this means incentivised action, regulations at a high level, and collaborative effort across multiple industries to leverage change in order to support fiber-to-fiber recycling and enable a closed loop solution for polyester fiber waste. On’s impact north star is to build a fair and inclusive future, driving progress on circularity and renewable materials. There’s a better way to do things.
“Our companies share an explorer spirit,” says On’s Dana Müller to Daniel Solomita, CEO of Loop Industries, as they come together with On’s Georg Singer to discuss collective solutions.
Loop Industries is one of On’s partners, a company that specializes in the fiber-to-fiber recycling space. Fiber-to-fiber recycling refers to the textile industry as a whole recycling its own polyester waste, hence the idea of the closed circle or ‘loop’.
Fiber-to-fiber recycling makes more ecological sense than sourcing PET from the beverage industry. Bottles can be recycled through conventional or mechanical recycling within a certain number of cycles (typically three) before the materials become too degraded, but if they’re processed into textiles, the cycles break there. Loop Industries has developed a technology to recycle low-value PET waste, including textiles, as well as plastic bottles that would have ended up in landfill or incineration otherwise.
“On is driving progress towards circularity paving the way for technologies that help to lower our footprint and reduce wasteful material use,” says On’s Georg Singer, “but at the same time meet our high quality standards that are required within the sportswear and performance industry.”
On believes that instead of breaking the loop of PET bottle recycling – where there is already a circular system in place in the packaging industry – the lifecycle of the footwear and apparel should be extended. Fiber-to-fiber recycling keeps footwear and apparel in the same industry – an aspiration for the scalable future of recycling.
“We started this mission to embed circularity into our processes, designs, and business models, back in 2022, with the launch of the Cloudneo shoe,” Singer continues. “The Cloudneo was the first shoe launched within our subscription program, Cyclon™, which is designed so the product can be easily returned to us to be recycled, so we can keep the recyclable materials in circulation.”
From here, On continues to seek innovative partners around the globe to support this vision. The collaboration with Loop Industries ultimately led to the recent launch of the Cloudeasy Cyclon shoe.The Cloudeasy Cyclon's upper is crafted from yarn made with Loop's 100 percent virgin-quality recycled polyester fiber, using the Infinite Loop™ technology.This innovation is part of a movement towards embedding circularity longer-term into what we do, and galvanize much-needed movement in this direction, across the industry-at-large.
“Through fiber-to-fiber recycling, On can take responsibility for our own products and reincorporate this into our production,” says Singer. “Growing regulation, especially in Europe, will force the packaging industry to use certain rates of recycled material, and also create scarcity for our industry to source recycled polyester from that industry.”
In 2023, recycled polyester accounted for 85 percent of On’s total polyester, largely coming from recycled PET bottles. Our goal is to reach more than 95 percent recycled or renewable PET fibers used in products manufactured in the year by 2027, where we aim to increase the use of fiber-to-fiber recycling. This is part of On’s wider strategy on Materials Innovation, where Preferred Materials is a key lever to achieving the goal of decreasing carbon emissions.
On’s partnership with Loop Industries is about better developing this new value and supply chain.
“We’ve had many challenges over the past few years,” The CEO of Loop Industries, Daniel Solomita, explains. “In textiles, there’s an enormous amount of what we call ‘contaminants’ in blends of fibers. That's really the tough part; having polyester mixed with nylon polyester, buttons, zippers, and different types of dyes.”
“Traditional [or conventional] recycling uses high temperatures to melt the plastic or very high pressure to break it apart,” he explains. “The issue here is that, besides breaking down the polyester, all of those different materials in construction will also all break down together. And when that happens, you have a tremendous amount of contamination left to deal with. This is why traditional textile recycling has never really been successful.”
Let’s start with a tasty analogy: Solomita simplifies the science using the example of a chocolate cake – eggs, flour, sugar, chocolate – that can be separated into its purest forms, built into a new chocolate cake, and then separated again.
In more detail, PET is a synthesis of petrochemicals, Monoethylene glycol (MEG) and Dimethyl terephthalate (DMT), both of which are derived from petroleum. “These are the two base building blocks that go into making PET for packaging and fiber applications,” says Solomita.
“It's simply a molecular chain – you have DMT molecules attached to MEG molecules and that molecular chain is what gives plastic its strength,” he continues.
“The Infinite Loop™ technology uses a low-temperature, catalytic process that cuts the bonds that hold those two petrochemicals together. We separate the DMT (a white solid) from the MEG (a liquid). We restore them back to their purest form using distillation columns. This brings us back to the virgin petroleum-based quality of DMT and MEG and then we can recombine them to make any finished product, that’s either a fiber or packaging application.”
Another one of the challenges Solomita sees on the supply chain is that the collection of post-consumer material, “isn't as developed yet as we would like it to be.”
Solomita makes clear the challenges around the post-consumer textile value chain, getting consumers to put those old clothes into a recycling bin, and then sorting them to be processed.
Singer poses the collective questions, “How do we get that material back? And how do we educate the consumer, that instead of throwing it in the garbage, you can now recycle that material?”
“Maybe we need in-store incentives through the retail network to get people to return textiles,” he continues. “As an industry, we also need to use less materials in construction. I think we need both factors to make that shift happen. The knowledge that waste actually has some value attached to it, can be a powerful tool.”
Right now, Loop Industries is looking at post-industrial sewing cuttings as another source of PET for fiber-to-fiber recycling. “We pay sewing factories for it, so it incentivizes them to gather, rather than incinerate it or leave it to landfill,” says Solomita. “It’s exciting to be able to create circularity around that type of material, especially in countries like India, Vietnam, and Bangladesh where that supply chain exists. Hopefully, the post-consumer supply chain will develop further too.”
Müller addresses scaling these solutions, “If you look at the entire value chain, is there one specific issue that’s the most important to fix, in order to reach scale?”
“I don't think all consumers connect how polyester, water bottles and petroleum all fit together [when we talk about recycling]," replies Solomita. “It'll be interesting if the consumer starts connecting that and starts demanding more sustainable materials and processes. That’s our hope, because it drives incentives for more circularity, and benefits everyone.”
“At On, we ask ourselves, where can we accelerate that process and what role can we play as a brand to tell the story?” says Müller.
This comes down to education, growing a global infrastructure behind fiber-to-fiber recycling, and incentives to reduce or reuse resources along the supply chain.
“We need government regulation to make sure that waste management companies will divert material from landfills and incineration and pull them out of those streams,” says Solomita. “And we need to continue to develop recycling technologies.”
The Cloudneo, Cloudrise and Cloudeasy Cyclon shoes, are proof points of the impact that industry collaboration can deliver. They set a precedent by showing what’s actually possible.
With change comes challenge. Every industry, at every level of the supply chain, plays their part. At On, we’re just at the beginning of leveraging long-term change towards a more circular future – collectively, there’s still much more to do.
Read the On Impact Progress Report, 2023 Loop Industries, founded in 2015, and based in North America, has developed an innovative fiber-to-fiber recycling technology, and aims to scale its Infinite Loop™ technology globally, providing fiber and packaging brands with a sustainable solution that helps meet their circularity goals.